- 2020-2-11
- Nessan Cleary 記事紹介
私は先週、東京で大野インクジェットコンサルティングの大野彰得氏主催の初の日本インクジェットビジネスコンファレンスに参加しました。これについて、この記事で説明します。
I spent most of last week in Tokyo for the inaugural Japan Inkjet Business Conference, organised by Aki Ohno of Ohno InkJet Consulting, and which I’m going to cover here in this story.
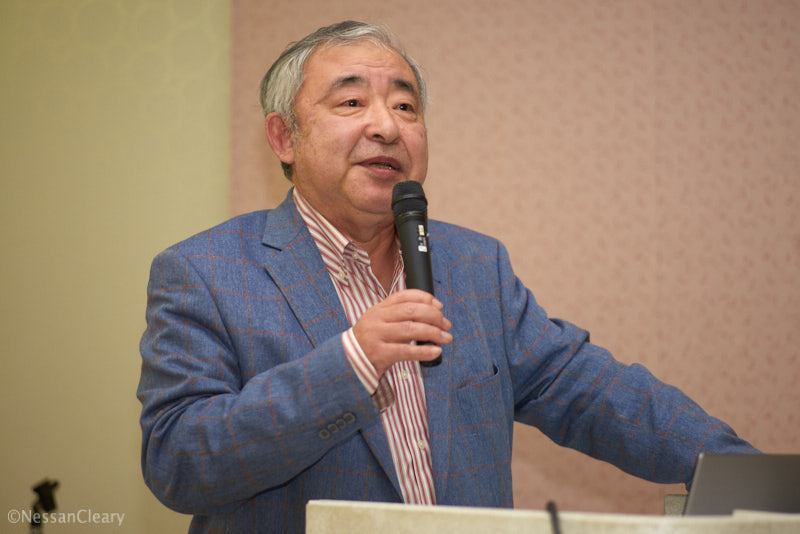
Akiyoshi Ohno, principal behind Ohno InkJet Consulting
大野インクジェットコンサルティングの代表、大野彰得
しかし、まず最初にちゃんと情報開示しておきますが、私は公平なオブザーバーとしてではなく、基調講演を行うためにそこにいたことを指摘しておく必要があります。日本の読者は、私サイトのの多くの記事が OIJCサイトでも公開されていることをご存知でしょう。(■ 大野註:Nessanは、ジャーナリストは「完全に中立公平」であるべきという哲学的原則をもっており、そういう意味では今回は基調講演を受けたり、コンサルタント協業しているというのは「完全に中立公平」ではない・・・という立場を明らかにしているわけです)
But in the interests of full disclosure, I should point out that for once I was not there as an impartial observer but rather to deliver the keynote speech. Japanese readers will know that many of the stories from this website are also published on the OIJC site.
ひとつのストーリーではカバーしきれないことも多いので、ふたつの部分に分割し、各要素を関連するコンテキストに入れるストーリーを作成できるように、さまざまなプレゼンテーションを単に順番に並べてコメントするということはしません。
There’s too much to get through in one story so I’m going to split it into two parts, and take the various presentations out of order so that I can create a narrative that puts each element into its relevant context.
当然、プレゼンテーションのいくつかはインクジェットプリントヘッドを中心に行われました。Fujifilm Dimatixの CEOである Martin Schoepplerが、特に Sambaヘッドとの関係で MEM技術の長所について語りました。一方、京セラのインクジェットデザインセンターのマネージャーである石倉慎は、バルクピエゾについて興味深い議論を行いました。
Naturally several of the presentations centred around inkjet printheads. Martin Schoeppler, CEO of Fujifilm Dimatix talked about the virtues of MEMs technology, particularly in relationship to the Samba heads, while Shin Ishikura, manager of Kyocera’s Inkjet Design Centre, argued for bulk piezo, which made for an interesting comparison.
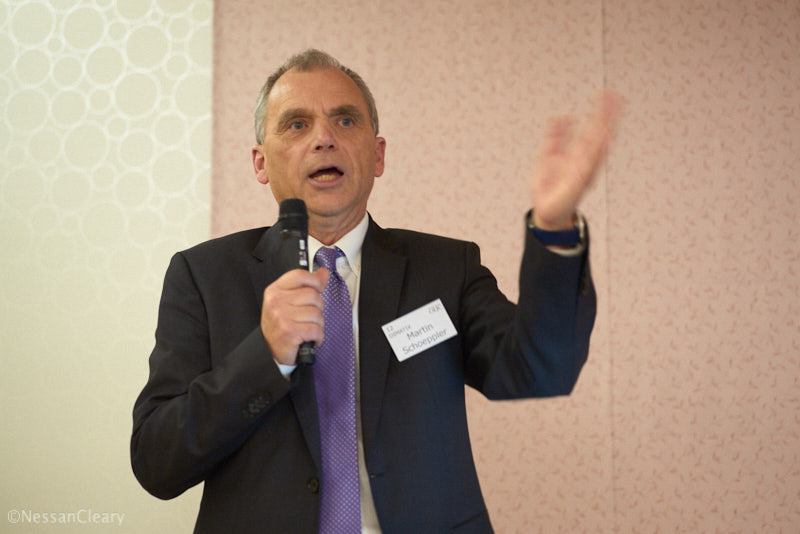
Martin Schoeppler, CEO and president of Fujifilm Dimatix
Fujifilm Dimatixの CEO兼社長である Martin Schoeppler
2006年に Dimatix(旧 Spectra)を買収した富士フイルムは、カリフォルニア州サンタバーバラに専用のシリコンファブ施設を設置するために多額の投資を行いました。ユーモアのセンスがイマイチの Schoepplerは、富士フイルムを「Dimatixにとって有難い資産」と評しています。彼は次のように述べています。「私たちは非常にハイテク志向です。長寿命で堅牢なテクノロジーを探しています。 コスト単価は重要だと思いますが、単に表面上のコスト(価格)ではなく、高くても長寿命だと、コストに対する考え方が違ってくるでしょう。プリントヘッドの寿命を確認する必要があります。」彼は、シリコンは非常に堅牢な材料でハイボリュームに対する要求にピッタリ合っていると言っています 。
Fujifilm, which acquired Dimatix (formerly Spectra) in 2006, has made a significant investment to set up a dedicated silicon fab facility in Santa Barbara, California. Schoeppler, who has a wry sense of humour, describing Fujifilm as a “good asset for Dimatix” says: “We are very high tech orientated. He states: “We look for the long life, robust technology. I think that cost per dollar is important but for me you have to see the lifetime of the printhead so that over time the cost is different.” He described silicon as a very robust material that’s very well-suited to the needs of high volume manufacturing.
全体として、Schoepplerは、ワイドフォーマット、産業、テキスタイルなど、いくつかの市場でインクジェットテクノロジーがどのように発展したか、そしてこの点で Dimatixがどのように位置付けられているかについて、明快な全体像を示しました。ここで詳しく説明するにはあまりにも詳細でしたが、後の記事で、特に MEMsプロセスの使用については Fujifilm Dimatixにまた触れることにします。
In all, Schoeppler gave a good overview of how inkjet technology has developed across several markets including wide format, industrial and textile, and of how he sees Dimatix’s place in this. It was too detailed to cover in depth here but I will come back to Fujifilm Dimatix in a later post, and in particular to its use of the MEMs process.
前述のように、京セラは異なるアプローチを採用しているため、石倉は新しい KJ4シリーズヘッドでバルクピエゾを使用する理由を説明しました。基本的に、これは、シリコンファブを構築するために必要な非常に高い投資コストと、シリコンウエハーでの比較的低い歩留まりと、ピエゾセラミックシートでの作業における京セラの実証済みの専門知識をベースとしています。
As noted, Kyocera has taken a different approach and so Ishikura described his reasons for using bulk piezo in the new KJ4 series heads. Essentially this comes down to the very high cost of investment necessary to build a silicon fab coupled with relatively low yields in Silicon wafers versus Kyocera’s proven expertise in working with piezo ceramic sheets.
石倉は、オリジナルの KJ4シリーズヘッドを初期のシングルパスプロダクションプリンターの多くに提供てきた京セラの役割を改めて表明し、市場は現在、より多くのスループットとレイダウン(インクの吐出量)、より高い堅牢度と、より少ないバラツキ、そしてより広いオペレーションウィンドウを求めていることを指摘しました。もちろん、価格を引き上げることなくという前提でです。昨年の IJCでの石倉のプレゼンテーションから、現在登場し始めたばかりの新しい KJ4EXシリーズを既に取り上げました。今年の後半には、このシリーズの詳細を書く予定です。
Ishikura reiterated Kyocera’s role in providing its original KJ4 series heads to many of the early single pass production printers, and then went on to point out that the market now demands more throughput and more laydown, with greater robustness and less variation as well as a wider operating window – all of course without pushing up the prices. I’ve already covered the new KJ4EX series, which is just starting to appear now, from Ishikura’s presentation at the IJC last year and I’m planning to write a deeper dive into this series at some point later this year.
Memjetの APAC地域でのビジネス開発担当上級副社長である Bent Serritslevから、新しい DuraLinkおよび DuraFlexヘッドを含む Memjetプリントヘッドの概要が提供されました。これらについてはすでに詳しく説明しましたが、Serritslevは Memjetが完全なプリントエンジンを開発したにもかかわらず、OEMが独自の製品を作成する余地があることを強調しました。彼は次のように説明しました。「彼らは、独自のワークフローとトランスポートシステムを持つことで、差別化できます。OEMは少しだけエレキ系の開発と、品質管理と必要な認証をやるくらいでいいと考えています。」
Bent Serritslev, senior vice president for business development in APAC region for Memjet, provided us with an overview of the Memjet printheads, including the new DuraLink and DuraFlex heads. I’ve already covered these in some detail but Serritslev did underline that even though Memjet has developed a complete print engine, there’s still room for OEMs to create unique products. He explained: “They can differentiate themselves by having their own workflow and transport system. We expect OEMs to do a little bit of electronics and they look after the quality control and any certification needed.”
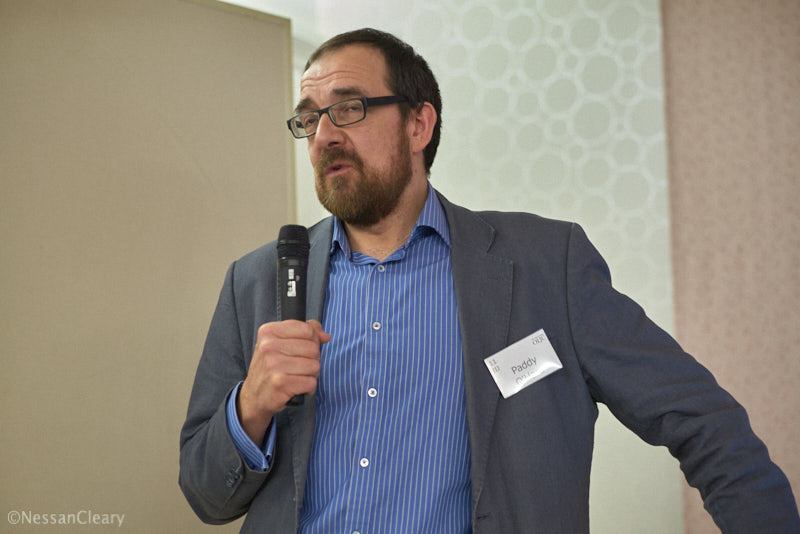
Paddy O’Hara, director of business development for Industrial InkJet.
パディ・オハラ、Industrial InkJetのビジネス開発ディレクター。
Industrial InkJetのビジネス開発マネージャーである Paddy O’Haraは、システムのインテグレーターによるプリントヘッドの見方を教えてくれました。彼は、KISSの原則 -Keep It Simple、Stupid-または Keep Inkjet Systems Simple-について話しました。「システムが複雑になるほど、開発期間が長くなり、失敗する可能性が高くなります。」とコメントしています。
Paddy O’Hara, business development manager for Industrial InkJet, gave us a system’s integrator view of printheads. He talked about the KISS principle – Keep It Simple, Stupid – or perhaps, Keep Inkjet Systems Simple – noting: “The more complex the system the longer the R&D and the more potential for failure.
IIJは、コニカミノルタヘッドのコンパクトなサイズを利用して、ほとんどのキットに簡単に収まる非常に小さなモジュール(プリントエンジン)に4つのカラーバーを収めます。オハラは、次のように付け加えました。「メディア搬送の為のアーチ形のプラテンや、や色の間のピニングは必要ありません。これにより生産性を高め、コストを削減できます。」彼はインクが重要であると指摘しました。手がかりはインクジェットという名にあります。「インクをテストするための多くのリソースを投入しています。インクサプライヤにインクを再調整して、希望どおりに機能させるようにします。コニカミノルタのヘッドが内部ヒーターとシンプルな波形を持っているので助かります。」
IIJ takes advantage of the compact size of Konica Minolta heads to squeeze four colour bars into a very small module that fits easily onto most kit. O’Hara added: “We don’t need the arch shape or pining between the colours, which gives higher productivity and lower cost.” He pointed out that ink is important – the clue is in the inkjet name – saying: “We put a lot of resource into testing the ink. We get the ink suppliers to reformulate the ink to make it work the way we like to work. It helps that the Konica Minolta heads have internal heaters and simple waveforms.”
もちろん、インクジェットにはまだ多くの課題があり、グローバルインクジェットシステムのビジネス開発マネージャーであるデビー・ソープは、ソフトウェアを使用してこの複雑さの一部に対処することについて次のように語っています。「ソフトウェアはシステムパフォーマンスを向上させ、問題を隠すことができます。これをリアルタイムで行うには、クローズドループシステムが必要です。」
Of course, there are still plenty of challenges in inkjet and Debbie Thorp, business development manager for Global Inkjet Systems, talked about using software to deal with some of this complexity, saying: “Software can improve system performance and can disguise problems. You need a closed loop system to do this in real time.”
彼女は次のように述べています。「プリントヘッドは素晴らしい技術ですが、必ずしも完璧ではありません。たとえば、ドロップサイズなどにばらつきがあり、バンディングエフェクトが発生する可能性があります。」と彼女は続けます。「従って、ノズル欠に対応したり、ステッチしたりするための戦略が必要です。またヘッドとインクは確実に適切な温度に保たれていることが必要です。」
She noted: “Printheads are a wonderful technology but they are not always perfect. There can be a variation in drop size and so on that, for example, can lead to banding effects.” She continued: “So you have to have a good strategy for missing nozzles, for stitching, and you need to make sure that the heads and inks are kept at the right temperature.”
彼女は、単色のフラットカラー(所謂フルベタ)をインクジェットで実現するのは難しいと指摘し、次のように付け加えました。「機能性材料のプリントの世界では、非常に均一なレイヤーを配置できるようにしたいわけですが、それはフルベタと同じ問題です。そのため、ステッチング、ノズル欠、クローズドループワークフローの検証と同じ戦略を使用します。」
She pointed out that solid flat colours are hard to achieve with inkjet, adding: “In the functional world we want to be able to put down a very uniform layer, which is the same problem as the solid flat colours. So we use the same strategies for stitching and for missing nozzles and verification for a closed loop workflow.”
また、Thorpは、ロボットアームを使用して長い吐出距離で自動車の部品(ウィングミラーのケーシング)にコーティングを施すビデオを示しました。彼女は次のように付け加えました。「ImageXpertの市場にとって非常に重要なツールを使用して波形開発することで、この距離を達成しました。」
Thorp also showed a video where inkjet was used to add a coating to an automotive part – the casing for a wing mirror – held by a robotic arm to present it to the head and with a long throw distance. She added: “We achieved this distance through wave form development using a tool that is very important to the market from ImageXpert.”
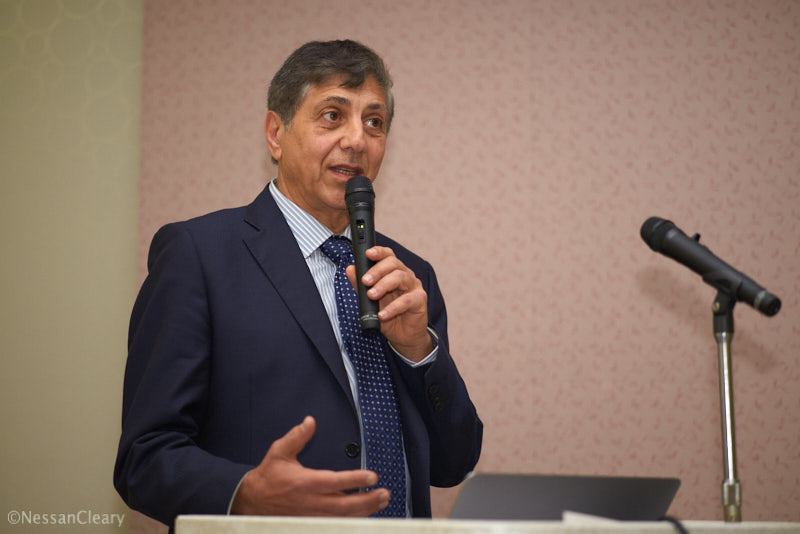
Yair Kipman, president of ImageXpert
ImageXpert社長 Yair Kipman
偶然にも ImageXpertの社長である Yair Kipmanも別のプレゼンテーションを行いました。ImageXpertは、その一連のドロップウォッチャーソリューションを通じてインクジェット印刷デバイスの開発において非常に重要な役割を果たしていますが、多くの読者や、そしてほとんどのプリンターおよびエンドユーザーはおそらくこの会社に気付いていないでしょう。ドロップウォッチャーを使用して、プリントヘッドから生成される液滴を撮影および分析します。これにより、システム開発者は、インクの配合を調整するか、粘度制御の温度と度合い、またはプリントヘッドの電子回路と波形を調整して、出力を微調整できます。キップマンは次のように説明しました。「1plの最小ドロップサイズで作業できます。これが、より小さなドロップサイズへという市場の方向です。」
As it happened, Yair Kipman, president of ImageXpert, also made a separate presentation. Many readers and certainly most printer and end users are probably not aware of this company, though ImageXpert plays an extremely important role in the development of inkjet printing devices through its range of drop watcher solutions. Drop watchers are used to film and analyse the ink drops as they are produced from the printheads, which allows systems developers to fine tune the output, whether by tweaking the ink formulation, or the temperature and degree of viscosity control or the printhead electronics and waveforms. Kipman explained: “We can work with 1pl minimum drop size – that’s the direction of the market towards smaller drop sizes.”
「GISを戦略的パートナーとして使用しているのは、自動波形最適化を行えるようにソフトウェアをオープンにしているからです。」同社は、標準のドロップウォッチャーをベースとして、シートフィードやロールツーロールなどのバリエーションも提供しています。また生産ラインに適合するように設計されたシステムもあります。キップマンは説明します:「それは非常にコンパクトです。そのため、朝にプリントする前に、すべてのノズルが同じ体積と速度で吐出していることを確認できます。」
He added: “We use GIS as a strategic partner because they have opened their software so we can do automatic waveform optimsation.” The company has developed a range of different solutions based around its standard drop watcher to handle different printers, such as sheetfed or roll to roll. There’s also a system designed to fit into a production line. Kipman explains: “It’s very small. So, before you print in the morning you can verify that all the nozzles are firing at the same volume and velocity.”
これは非常に特殊な分野であるため、それ自体で別の話をする価値がありますが、Fespaと Drupaがまだ来ないので、これを理解するには時間がかかるかもしれません。
This is such a specialized area that it’s worth a separate story in its own right, though with Fespa and Drupa still to come this might take me a while to get around to.
見落とされることが多いもうひとつの重要なコンポーネントは、KNF Japanのセールスマネージャーである細畑信彦氏が議論した、印刷システムの周りにインクを供給するために使用されるポンプです。KNFはダイアフラムベースの設計を採用しています。これは適度にコンパクトで、メンテナンスがほとんど不要で長寿命です。彼は、ナノ粒子と高顔料負荷を特徴とする新しいインクと、銀粒子または有機ポリマーを含む導電性インクなどの機能性インクを備えた高速プリンターへの現在の傾向が、すべてポンプに問題を引き起こすことを説明しました。これは主に、顔料粒子によるアブレーション、改善された耐薬品性の必要性、および流動性の低いより高粘度のインクに対処する必要性にまで及びます。その結果、KNFは、これらの問題に対処するために5つのダイヤフラムを備えた新しい FP150および FP400シリーズポンプを導入しました。
Another vital component that’s often overlooked is the pumps that are used to push the ink around a print system, which Nobuhiko Hosobata, sales manager for KNF Japan, discussed. KNF uses a diaphragm-based design, which is reasonably compact and gives long service life with little maintenance necessary. He described how the current trends towards faster printers with new inks featuring nanoparticles and high pigment loads as well as functional inks such as conductive inks with silver particles or organic polymers, all cause problems for pumps. This is mainly down to ablation through the pigment particles as well as the need for improved chemical resistance and the need to cope with higher viscosity inks that have less flow. Consequently KNF has introduced a new FP150 and FP400 series pumps that feature five diaphragms to cope with these issues.
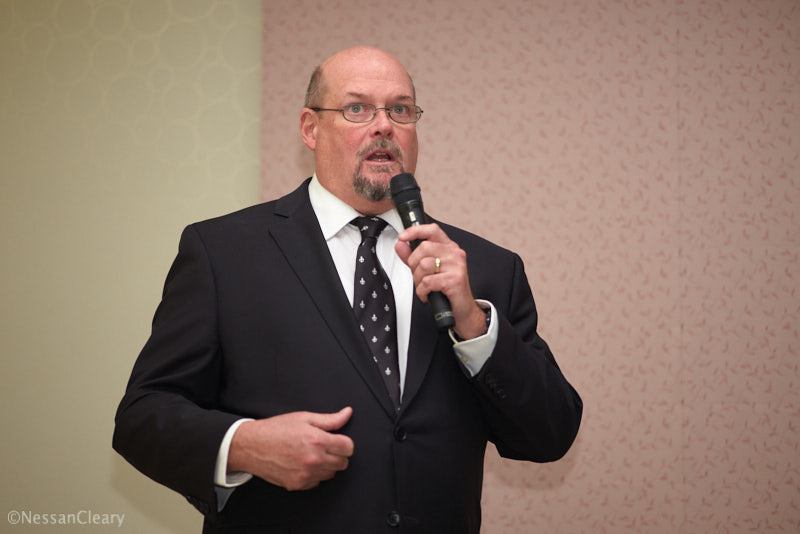
Michael Beck, vice president of worldwide sales for Phoseon
フォセオンの世界販売担当副社長、マイケル・ベック
Phoseonのワールドワイド販売担当副社長 Michael Beckは、UVインクを硬化させるために水銀ランプではなく LEDを使用することの利点について話しました。彼は、水銀ランプの硬化を管理する特許の一部が 100年以上前のものであると指摘し「2002年に Phoseonが LED製品の製造を開始したとき、それは決して機能しないと言われました。」しかし、今日では LED硬化が広く使用されています。高いエネルギー節約やオペレーターへのリスクの低減など、多くの利点を備え、そしてもちろん、LEDは通常、統合された印刷システムの寿命を持続させます。
Michael Beck, vice president of worldwide sales for Phoseon, talked about the advantages of using LEDs rather than mercury lamps to cure UV inks. He pointed out that some of the patents governing mercury lamp curing are over a hundred years old, adding: “So when Phoseon started making LED products in 2002 we were told that it would never work.” But nowadays LED curing is widely used in most print markets with a number of benefits, including high energy savings, as well as lower risk to operators, and of course, LEDs will typically last the lifetime of the print system they’re integrated with.
Phoseonは、より多くの光開始剤の使用を可能にする非常に低い波長のランプを可能にする UVCと、水性インクを乾燥させる興味深いオプションを提供する近赤外または NIRも検討しています。
Phoseon is also looking into UVC, which allows lamps with very low wavelengths that would lead to more photo initiators, and Near InfraRed or NIR, which offers an interesting option for drying water-based inks.
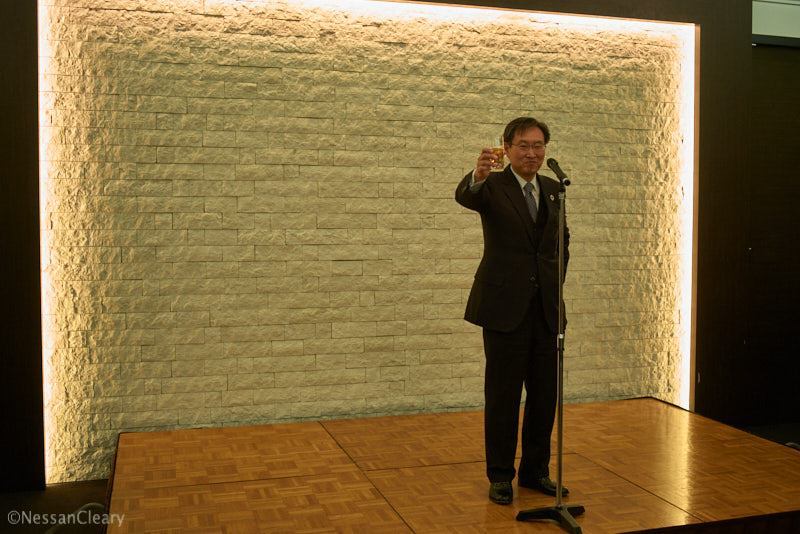
Minoru Usui, president and CEO of Epson addresses the networking event.
エプソンの代表取締役社長である臼井実氏がネットワーキングイベントについて語ります。
残りのプレゼンテーションについては2番目のレポートで説明しますが、このイベントの全体的な雰囲気は非常に好意的なものであったことを指摘する価値があると思います。日本のインクジェット業界のリーダーであり、リコー、スクリーン、コニカミノルタなど、ほとんどの企業の代表者がいます。 しかし、大野は日本のインクジェット産業をひとつのフォーラムにまとめるという彼の目標を達成したように見えます。いずれにせよ、次のイベントが発表される前であっても、そこにいる全員がすぐに次のイベントに参加する計画を立て始めると、イベントが成功したことがわかります。
I’ll cover the rest of the presentations in a second report but I think it’s worth pointing out that the overall vibe from this event was very positive, not only because the conference was packed with 175 delegates, but also because the event attracted many of the leaders of the Japanese inkjet industry, with representatives from most companies including Ricoh, Screen, Canon and Konica Minolta – well, too many to mention them all. But it certainly looks as if Ohno achieved his aim of bringing together the Japanese inkjet industry into one forum. In any case, you know that an event has been successful when everyone there immediately starts making plans to attend the next one even before it’s been announced!