- 2019-9-16
- トピックス
英国ケンブリッジ郊外に拠点を置く Industrial Inkjet社(IIJと略すことも多い)は、社長の John Corrall氏以下、従業員数約60名+で、私が前職時代に設立を支援した経緯もあり、コニカミノルタヘッドを採用したプリントエンジンの開発・製造・販売をを行うインテグレーターです。一品料理的カスタム開発も受託しますが、これまで10年間+の経験値の蓄積から、基本部分はプリントエンジンとして標準品に纏め、顧客の事情に応じた部分をカスタマイズするという効率化を図っています。
こちらのサイトに、時折興味深い記事が掲載されます。今回は「既存アナログ印刷機に、後付けでインクジェットのプリントエンジンを追加する際のノウハウ」について書いているので、Johnの了解を貰って翻訳記事をアップしました。
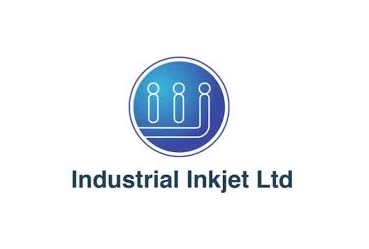
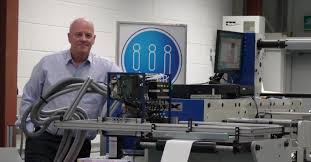
Managing Directer Mr.John Corrall
数年前、インクジェット関連の会社(ここケンブリッジで私たちからそれほど遠くない場所にある)の CEOは、すぐに「すべての印刷物がデジタルになる」と言ったそうです。当社 Industrial Inkjet Ltd(IIJ)では、物事の見方が少し異なります。私たちの予測は、「採算計算が合うまでは何もデジタル化しない」と「何百万ものものを印刷したいならデジタルは道ではない」という線に沿っているでしょう。特に 2番目の声明は、インクジェット会社からは少し奇妙に思えるかもしれませんが、ハイブリッドラベル印刷機が今日のラベル市場で必需品である理由を説明しています。
Some years ago, the CEO of an inkjet company (located not so far from us here in Cambridge) was quoted as saying that soon “all print will become digital”. At Industrial Inkjet Ltd (IIJ) we see things a little differently. Our predictions would be more along the lines of “nothing goes digital until the economics work” and “if you want to print millions of anything then digital isn’t the way”. The second statement in particular may seem a little strange from an inkjet company, but it explains why the hybrid label press is today’s must-have item in the label market.
この記事は、従来のラベル印刷機をハイブリッド印刷機に転換する際の技術的な問題の一部を説明するために書かれていますが、最初に「何百万もの」という言葉についてもう少し説明する必要があります。
This article is written to explain some of the technical issues involved in converting a conventional label press into a hybrid press, but first we should explain a little more about the “millions of anything” statement.
2011年に、当社はスウェーデンの Lundens Tryckeriという会社の Mark Andyフレキソ印刷機にカラーインクジェットモジュールを取り付けました。比較的小さな印刷会社ですが、Lundensはラベルコンバーティング市場がどのように変化しており、それがビジネスの将来にどのように影響するかを理解しているという点で非常に先見的でした。彼らとの最初の会議で、彼らは、ジョブランの長さが継続的に減少している一方で、種類は増加している(多品種少量に向かっている)と説明しました。生産されるラベルの総数は減りませんでしたが、それらを生産する手間は継続的に増加しました。ツーリング(版の製作)とセットアップ時間が支配的でした。簡単に言えば、彼らはやっていた短期の小バッチ作業の多くで損失を出していましたが、その仕事を受けなかった場合、彼らはまだ利益を上げることができる大きな仕事も貰えなくなるという状況でした。Lundensは「純粋な」デジタル印刷機を検討していましたが、ハイエンドラベルの非常に短いジョブに対してのみ経済的であると計算していました。彼らは、非常に短いまたは非常に長いランレングスで経済的であるだけでなく、その間のすべてのジョブでも経済的なプレスの必要性を見ました。彼らのアイデアは、既存の Mark Andyにインクジェットを追加することでした。大規模な仕事では、従来のフレキソ印刷機として使用します。小さな仕事では、彼らはインクジェットのみを使用します。そして(当時の私たちにとっては新しいアイデア)いくつかの仕事については、彼らは「ミックスアンドマッチ」をするのです。たとえば、同様のラベルの「セット」を作成する場合、すべてに共通の背景色にフレキソを使用し、変更が必要な画像とテキストにデジタルを使用するのです。
Back in 2011 we installed a colour inkjet module onto a Mark Andy flexo press for a company called Lundens Tryckeri in Sweden. Although a relatively small print company, Lundens turned out to be quite prescient in their understanding of how the label converting market was changing and how it would affect the future of their business. In the first meeting with them they explained that job run lengths were continuously falling while variation was increasing. The total number of labels being produced wasn’t falling, but the hassle to produce them continuously increased. Tooling and setup time dominated. Put simply, they were making a loss on a lot of the short-run small-batch work they were doing, but if they refused it then they wouldn’t be given the larger jobs with which they could still make a profit. Lundens had looked at “pure” digital presses but had calculated that they would only be economic for very short runs of high-end labels. They saw the need for a press that was not only economic on very small or very large run lengths, but also on all those jobs in between. Their idea was to add inkjet to their existing Mark Andy. On large jobs they would use it as a conventional flexo press. On small jobs they would use only the inkjet. And (a new idea to us at the time) on some jobs they would mix-and-match. For example, in producing “sets” of similar labels they could use flexo for the background colours which were common to all and use digital for the images and text that needed to change
インストールから約 1年後、Lundensの Bosse Nielsenから下のグラフが送られてきました。彼のコンセプトはうまく機能しており、インクジェットモジュールの使用から従来のフレキソ印刷機としての印刷機の使用に変更すべき明確な経済的クロスオーバーポイントを見ていました。私たちにとって、これが「ハイブリッド」の利点の理解の始まりでした。
About 1 year after the install, Bosse Nielsen of Lundens sent us the graph below. His concept had worked and he was seeing a clear economic cross-over point at which he should change from using the inkjet module to running the press as a conventional flexo machine. For us this was the start of our understanding of the benefits of “hybrid”.
現在、当社はこのような印刷機を 30台以上設置しており、技術的な問題については十分な経験を積んでいます。また、スタンドアロンのデジタル印刷機メーカーのほとんどが、デジタルだけでは何百万ものジョブを印刷する方法ではないということに気が付き、独自のハイブリッドソリューションを提供していることを知ったことも非常に興味深いことでした。
We have created over 30 such presses now and we have a good deal of experience of what the technical issues will be. Its also been very interesting for us to see how most of the stand-alone digital press manufacturers have also realised that digital by itself isn’t the way to print the “millions” of jobs and they now offer their own hybrid solutions.
IIJでは、ハイブリッドインクジェットソリューションを機能させるためには、多くの技術的な課題があることを認識しています。弊社が販売するソリューションでは、知識と柔軟なアプローチにより、これらに対する責任を負っています。ただし、ソリューションに何が入っているのかを理解してもらうために、これらの課題が何であるかを理解するために時間をかけることは意味があります。
At IIJ we recognise that there are a number of technical challenges involved in making a hybrid inkjet solution work. On any solution we sell, we take responsibility for these, through our knowledge and flexible approach. However, it’s worth taking the time to understand what these challenges are in order to appreciate what goes in to our solution.
ハイブリッドの問題
Hybrid Issues
ハイブリッドプレスの作成と実行に関する技術的な問題は、一般に次の 3つの分野に分類されます。
The technical issues about creating and running a hybrid press generally fall into three distinct areas:
インクとメディアの相互作用
機械的相互作用
カラー管理とワークフロー
Ink and Media interaction
Mechanical Interaction
Colour Management and Workflow
1.インクとメディアの相互作用
1.Ink and Media interaction
お客様をフレキソのみからハイブリッドに変換する際の一般的な問題は、UVインクジェットインクでは通常の標準メディアがまったく機能しない場合があることです。フィルムストックでは、通常、問題はメディアの表面エネルギーにあります。通常、44ダインの表面エネルギーで十分ですが、ラベルプロデューサーが表面エネルギー 30台のダインレベルのプラスチックフィルムストックを私たちに見せることもしばしばあります。これらにそのままプリントすることはできません。
A common issue when converting a customer from flexo-only to hybrid is that their normal standard media may not work at all well with UV inkjet inks. On film stocks the problem usually comes down to media surface energy. A surface energy of 44 dynes is typically enough, but it’s very common for label producers to show us plastic film stocks with dyne level in the 30’s. These we simply can’t print as they are.
顧客は、お気に入りのメディアのどれが問題なく機能するか、また、典型的な画像ファイルの場合のプリントあたりのコストを知る必要があります。したがって、印刷サンプルテストでは、多数の顧客画像を各メディアに印刷します。顧客は許容できる品質をチェックでき、ソフトウェアから印刷単価を引き出して、手頃な価格であることを確認できます。
The customer needs to know which of his favourite media will work OK and also what the cost-per-print will be for typical image files. So, in the print sample tests we will print a number of customer images onto each of his media. The customer can check for acceptable quality and we can pull the cost-per-print from the software so that he can check that it is affordable.
メディアがうまく機能しない場合は、解決策を見つけようとします。これは、コロナなどの前処理を使用することによる場合がありますが、印刷解像度またはインク密度の変更も実験します。さまざまなインクジェットインクを試します。また、UV硬化遅延の調整を試みます(以下を参照)。
Where the media doesn’t work well, we will try to find a solution. This may be by using pre-treatment such as corona, but we will also experiment with changes of print resolution or ink density. We will try different inkjet inks. We will also try adjusting the UV cure delay (see below).
インクジェットプリントヘッドの後の UVランプの位置は非常に重要です。インクがメディアに適切に濡れるように最適な遅延のポイントがあります。薄いフィルムであるため、使用されるインクの総量は少なくなります。つまり、コストが削減されます。
The position of the UV lamp after the inkjet printheads is quite critical. There is an optimum delay to allow the ink to wet out properly onto the media. Because it’s a thin film the total amount of ink used is low – which means less cost.
2.メカニカルインテグレーション
2. Mechanical Integration
おそらく、インクジェットをフレキソ印刷機(または任意のウェブ印刷機)にインテグレートする際の最大の問題は、ウェブのふらつきやメディアの伸びにどう対処するかです。
Possibly the biggest issue when integrating inkjet onto a flexo press (or any web press) is how to cope with web wander or media stretch.
既存の印刷機にインクジェットを追加することを検討しているお客様は、通常、ウェブが横にゆらぐと色と色のポジショニングが不正確になることを容易に理解してくれます。これは、使用されている印刷技術に関係なく同じです。一般的に、彼らはまた、異なる色のインクジェットバーをウェブに広げると、これが問題を引き起こしていることを把握します。色の間のギャップ(距離)が大きくなることは、ウェブが色の間を通過するときに横に移動する時間が長くなることを意味します。大まかに言えば、インクジェットプリントバーを取り付けるウェブの長さを 2倍にすると、色と色のポジションのエラーが 2倍になる可能性があります。
Customers considering adding inkjet to an existing press usually have no trouble to understand that if the web wanders sideways then the colour-to-colour registration will be inaccurate. This is the same whatever print technology is in use. Generally, they also grasp that if you spread out the different colour inkjet bars down the web then this is asking for trouble. Big gaps between colours means that there is more time for the web to move sideways as it passes between them. Roughly speaking if you double the length of web over which you mount the inkjet print bars then you are likely to double the error in the colour-to-colour registration.
色間の位置合わせエラーの解決策は、インクジェットユニットを非常にスリムにし(ウェブに沿ってスペースをほとんど占有しない)、その方法でエラーを最小限に抑えるか、これが不可能な場合は代わりにWebトランスポートの非常に正確なセクションを印刷機に追加することです。それはオリジナルの印刷機よりもはるかに正確なものが必要です。後者の解決策は、印刷機の大手術を意味する可能性があり(効果的に半分に切断し、まったく新しいセクションを挿入する)、多くの追加コストが発生します。 IIJでは、非常にスリムでコンパクトなコニカミノルタのプリントヘッドを使用できるという利点があります。標準のインクジェットモジュールでは、最初の色から最後の色までのウェブ下方向の総距離はわずか 140mm(5.5インチ)であるため、ウェブの横揺れによるエラーを最小限に抑えます。
The solution to colour-to-colour registration error is then to either make the inkjet unit very slim (takes up very little room along the web) and minimise the errors that way, or if this is not possible then instead to add into the press a very accurate section of web transport – significantly more accurate than the original press itself. The latter solution can mean major surgery to the press (effectively cutting it in half and inserting a whole new section) and adds a lot of cost. At IIJ we have the advantage of using Konica Minolta printheads which are very slim and compact. In our standard inkjet modules, the total distance down-web from the first colour to the last colour is only 140mm (5.5inches) – so minimising any errors due to sideways wander of the web.
メディアストレッチは、印刷エラーの潜在的な原因でもあります。この場合、異なる色のインクジェット印刷バーを距離をあけて取り付けると、問題が発生する可能性があります。私たちの解決策は、すべての色のプリントヘッドを単一の配列に非常に近づけることです。
Media Stretch is also a potential cause of print errors. In this case mounting the different colour inkjet print bars far apart could cause issues. Our solution is to have the printheads for all colours very close together in a single array.
メディアストレッチに関連する重要なポイントは、シャフトエンコーダーの位置です。シャフトエンコーダーはウェブ速度を測定し、インクジェットユニットの発射周波数を制御します。これにより、ウェブ速度に関係なく、各画像が正確な長さで正確に印刷されます。これは、インクジェットユニットでウェブの速度がわかっている場合にのみ正しく実行できます。シャフトエンコーダーがプレスの少し下または上に取り付けられている場合、その時点での張力は、インクジェット下の張力とは異なる可能性があります。これは、シャフトエンコーダーが間違った速度を認識しており、インクジェットが正しく印刷されないことを意味します。ラベルが本来の大きさよりもわずかに大きいか小さいかは気付かないかもしれませんが、色が完全に揃っていない場合は必然的に気付くでしょう。
An important point related to media stretch is the location of the shaft encoder. The shaft encoder measures the web speed and controls the firing frequency of the inkjet unit. It ensures that each image is printed exactly the correct length – whatever the web speed. It can only do this correctly if it knows the web speed right at the inkjet unit. If the shaft encoder is mounted some distance down or up-web on the press then the tension at that point is likely to be different to the tension under the inkjet. That means that the shaft encoder is seeing the wrong speed and the inkjet will print incorrectly. The customer may not notice if the label is very slightly larger or smaller than it should be, but inevitably he will notice if the colours don’t quite align.
顧客が非常に心配する傾向がある問題は、インクジェット印刷の同期です。これは、後でダイカットされる領域内にインクジェットプリントが正しく配置されていることを確認している可能性があります。または、インクジェットプリントがメディア上のフレキソプリントまたは他のプリプリントと位置が整合している必要がある場合があります。
An issue that customers tend to worry about a lot is synchronising the inkjet print. This might be making sure that the inkjet print is placed correctly within the area that will later be die-cut, or it may be that the inkjet print has to line up with the flexo print or other pre-print on the media.
実際には、これらの問題が私たちに困難を与えることはめったにありません。ダイカッターと同期する必要がある場合、実際には、ダイカッターの後、およびバッキング(剥離紙)が剥離された後に、フォトセンサーを取り付けることが重要です。各ラベルにトリガーマークとして使用できる繰り返し印刷があるかどうかわからない場合は、裏紙に対してラベルストックを見るセンサーを使用できる場合があります。
In practise these issues rarely give us much difficulty. If we need to synchronise to the die-cutter then the trick is actually to mount the photo-sensor after the die cutter and after the backing has been stripped. If we can’t be sure that each label will have repeatable print which we can use as a trigger mark then we may be able to use a sensor that sees the label stock against the backing material.
インクジェットの後にトリガーセンサーを配置すると、(インクジェットの前にある必要があると考えている)顧客を混乱させる可能性がありますが、実際にはうまく機能します。ただし、新しい印刷ジョブを開始すると、いくつかの無駄が発生します。インクジェットからダイカッターを介してフォトセンサーまでの距離に相当するウェブの長さは、印刷されません。
Placing the trigger sensor AFTER the inkjet can confuse customers (who expect that it must be before the inkjet) but it can actually work well. However, on starting any new print job there will be some waste generated. A length of web equivalent to the distance from the inkjet through the die cutter to the photo-sensor will go unprinted.
素材の継ぎ目を避けることも潜在的に重要な問題です。材料のテープ結合は、インクジェットヘッドとインクジェット下のプレートの間に収まらない場合があります。テープによるメディアの結合部がウェブによってこのギャップに高速でドラッグされると、重大な損傷が生じる可能性があります。このため、継ぎ目回避リフティングメカニズムを開発しました。レーザー光線は、ウェブの上面のすぐ上で照射されます。インクジェットの上流にある程度の距離が必要です。レーザービームが邪魔された場合(継ぎ目だけでなく、折り目や波紋、あるいは汚れ)、レーザーがリフトメカニズムをトリガーし、プリントヘッドを邪魔にならない位置に移動させます。問題部分がインクジェット部分を通過するとすぐに、プリントヘッドが元の位置に戻り、印刷が再開されます。プリント速度はもはや問題ではなくなりました。2011年には、ほとんどのインクジェットラベルシステムは、インクジェットから 1分あたり約 25〜30メートルの最大印刷速度に制限されていました。通常のフレキソ速度よりもかなり遅いですが、ショートランではこれは大きなハンディキャップではありませんでした(インクジェットとダイカットが同期するまでにジョブは終了しました)。2012年から、インクジェット速度は毎分 50から 80メートルの範囲に増加し、現在は 100メートル/分になっています。ラベルの場合、これは他のプロセスの最大速度に追いつくか、それを超えるのに十分です
Avoiding a splice in the material is also a potentially important issue. A taped join in the material might not fit between the inkjet heads and the plate under the inkjet. If the join is dragged into this gap at high speed by the web then significant damage could result. For this reason, we developed a splice avoidance lifting mechanism. A laser beam is shone across the web just above its top surface. It needs to be some distance upstream of the inkjet. If anything breaks the laser beam (a splice but also a crease or ripple, or perhaps just some dirt) then the laser triggers the lift mechanism which moves the printheads up out of the way. As soon as the problem has moved past the inkjet then the printheads are lowered back into position and printing restarts. Speed as an issue has really gone away. Back in 2011 most inkjet label systems were limited to a maximum print speed of around 25 to 30 metres/minute from the inkjet. Although substantially slower than typical flexo speeds, for short runs this wasn’t a great handicap (by the time the inkjet and die-cut were synchronised the job was finished). From 2012 inkjet speeds increased into the range 50 to 80 metres per minute, and they are now at 100metres/minute. For labels this is good enough to keep up with or even exceed the maximum speeds of other process that are typically in line with the printing process.
3.カラーマネジメントとワークフロー
3. Colour Management and Workflow
インクジェット技術と経験が向上するにつれて、新しいインクジェットシステムの購入に伴うリスクは着実に減少し続けています。顧客は、潜在的な機械的な問題について今ではあまり心配せず、代わりにソフトウェアについてもっと心配しています。オペレーターによるシステムの実際の使用方法、または印刷ジョブの正確な見積もり、適切な印刷準備、顧客の期待に応じた印刷、迅速な出荷、プロセス全体の追跡とモニタリングを保証するために必要な ITシステムに集中します。
As inkjet technology and experience has improved the risk involved in buying a new inkjet system has continued to reduce steadily. Customers worry a lot less now about potential mechanical problems and instead worry a lot more about software. They concentrate on how the system will actually be used by the operator, or what IT systems they will need to ensure that print jobs are quoted accurately, prepared for print properly, printed to the customer’s expectation, shipped promptly and the whole process is tracked and monitored
ラベル市場では、印刷機全体を単一画面で制御するとか、オペレーターの役割のスキルの軽減とか、顧客の注文から印刷までのプロセスは通常完全に無人で行われることを期待するとかいう傾向が見られます。これは私たちが今日取り組んでいるものです。
In the label market we see a trend towards single-screen control of the whole press, deskilling of the operator’s role and an expectation that the process from their customer’s order to print will normally be completely hands-off. This is something we are working on today.
当社の標準ソフトウェアには多くの強力な機能が含まれていますが、セットアップと構成には使用可能なパラメーターが多すぎるため、オペレーターが時間をかけて詳細を学習することはできません。
Although our standard software includes a lot of powerful capability, the setup and configuration simply has too many parameters available to expect an operator to take the time to learn it in detail.
硬化遅延(プリントしてから UVランプで硬化させるまでの時間)が正しいことを確認し、色間の「ピン止め」を回避し、ウェブの高解像度を使用することにより、IIJエンジンによって生成されるインク層が他よりも薄くなり、ラベルあたりのコストを大幅に節約できます。単色ブラックの最大化などのインク節約機能を備えたワークフローソフトウェアを追加することにより、さらに節約できます。これは、ハイブリッドモジュールの投資収益率が非常に短くなり、インクジェットがフレキソと競合しないランレングスが何万ものラベルに及ぶ可能性があることを意味します。(■ 大野註:IIJ社は永年の経験の結果、高速でメディアを搬送し、各色ヘッド間の距離を極限まで短くできるコニカミノルタのスリムなヘッドを使用し、液滴のジェットから UV照射までの時間を最適化することで、所謂ピニング(中間硬化)は不要としています)
By ensuring the cure delay is correct and avoiding “pinning” between colours, and by using high print resolutions down web, we find that the ink layer produced by an IIJ engine is thinner than others, giving a significant cost saving per label. By adding workflow software with ink saving functions such as maximising single colour black, there can be even further savings. This can mean that the return on investment for a hybrid module can be very short and the run length at which inkjet is un-competitive against flexo can be extended to many tens of thousands of labels.
まとめ
Summary
過去 8年間は、スウェーデンの友人が世界の他のほとんどの地域よりもずっと前にハイブリッド印刷機の光を見たことを示しています。本質的に、彼はフレキソ印刷とデジタル印刷の経済性のギャップを把握し、古い印刷機にインクジェットを追加することで、これまでにないショートラン印刷の圧迫に耐えることができることに気付きました。IIJの哲学は常に「シンプルに保つ」ことであり、既存の印刷機にインクジェットを追加する際に、スリムで正確なコニカミノルタプリントヘッドを使用することで、印刷機で大手術を行う必要がなくなりました。その代わりに、非常にコンパクトなカラーモジュールを追加します。このモジュールは、その性質上、メディアの横揺らぎやストレッチなどの問題を解決する証拠となります。フレキソ印刷機の大規模な市場設置ベースにより、既存のほとんどすべての印刷機をアップグレードし、経済性を大幅に向上させ、寿命を延ばし、顧客の能力を変革する経験が当社にはあります。
The last eight years have shown that our friend in Sweden saw the light of hybrid presses long before most of the rest of the world. Essentially, he grasped the gap in the economics between flexo and digital print and realised that adding inkjet to his old press would enable him to survive the squeeze of ever shorter runs. IIJ’s philosophy has always been “keep it simple” and in adding inkjet to existing presses the use of slim, accurate Konica Minolta printheads allowed us to escape the need to perform major surgery on the press. Instead we add a very compact colour module that by its nature is proof against issues such as web-wander or stretch. With a large installed base on a wide range of flexo presses we have the experience to upgrade almost any existing press, greatly improving its economics, extending its life and transforming the customer’s capability
【参考記事】Industrial Inkjet社のプリントエンジンをフレキソラベル印刷機に組み込んだ事例
FOCUS社 ハイブリッド・ラベルプリンター:フレキソ+インクジェット