- 2019-11-25
- Nessan Cleary 記事紹介
このストーリーは先週の新しいプリントヘッドに関するストーリーの直接的な続編であるため、Industrial Inkjet(IIJ)のビジネス開発ディレクターである Paddy O’Haraが説明したように、コニカミノルタの新しい KM1280iMHH-Sから始めるのが賢明でしょう。
The IJC pt2: From printhead modules to the new KM1280iMHH-S
Since this story is a direct follow-on to last week’s story about new printheads, it seems sensible to start with Konica Minolta’s new KM1280iMHH-S, as discussed by Paddy O’Hara, director of business development for Industrial Inkjet, or IIJ.
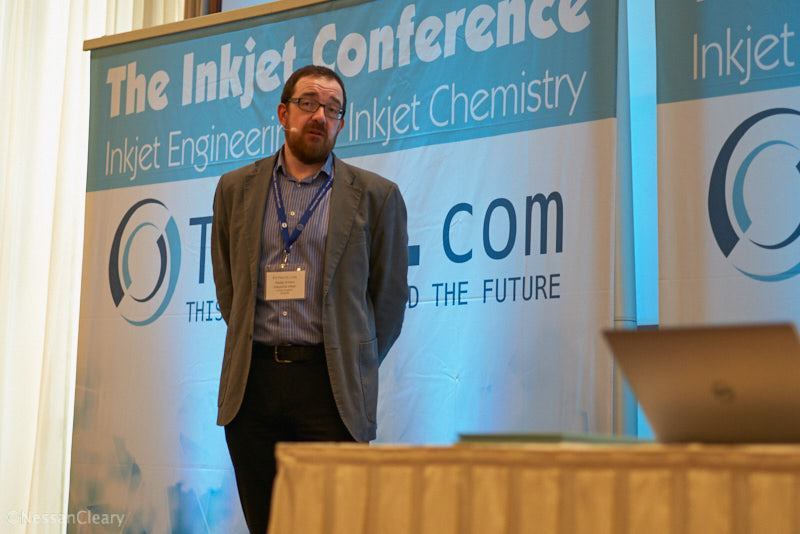
Paddy O’Hara, director of business development for Industrial Inkjet.
Paddy O’Hara インダストリアルインクジェットのビジネス開発ディレクター
コニカミノルタのプリントヘッドのほとんどは、コーディングおよびマーキングアプリケーション用に 100〜400dpiの解像度で大きなドロップを生成するか、高品質グラフィックス用に 600〜1200dpiで小さなドロップを生成します。したがって、KM1280iMHHはポートフォリオの中央に収まるように設計されており、1280ノズルから中程度のドロップサイズで 450dpiを生成します。最初のリリースは、シングルパスの可変データアプリケーション向けのバージョンで、高速では十分な大きさのドロップを生成できますが、細かいテキストには十分な解像度があります。また、白色およびスポットワニスの印刷に使用できるだけでなく、ダイレクトシェイプ印刷(平面ではない物体への直接プリント)、およびインク以外の液体出射用途にも使用できます。
Most of Konica Minolta’s printheads produce either large drops at 100-400dpi resolutions for coding and marking applications, or small drops at 600 to 1200 dpi for high quality graphics. So the KM1280iMHH is designed to fit in the middle of the portfolio, producing 450dpi with a medium drop size from 1280 nozzles. The first release will be a version for single pass variable data applications, where it can produce large enough drops for higher speeds, but with enough resolution for fine text. It can also be used to print white and spot varnish as well as for direct to shape printing, and materials deposition uses.
この一連のヘッドは、シリコンノズルプレートを備えており、高速での着弾精度が向上します。プリント幅は 72mmで、450npiで、通常の発射周波数 40KHzでネイティブの 10plドロップボリュームを生成できます。粘度 7〜12 mPa•sの溶剤、オイル、UVおよび水性インクを処理でき、内部ヒーターのオプションもあります。また、KM1024iシリーズと同じフットプリントを持ち、同様のドライブエレクトロニクスを使用しているため、かなり簡単にインテグレーションできます。来年発売予定です。
This series of heads will feature a silicon nozzle plate for better drop accuracy at higher speeds. It has a print width of 72mm, with 450npi, able to produce a native 10pl drop volume with a typical firing frequency of 40KHz. It can handle solvent, oil, UV and aqueous inks, with a viscosity of 7-12mPa•s and theres also an option for an internal heater. It also has the same footprint of the KM1024i series and uses similar drive electronics so that it should be possible to integrate fairly easily. It’s due to be available next year.
O’Haraは、IIJがコニカミノルタと約10年にわたって仕事をしており、これらのプリントヘッドを英国市場に供給することと並んで、インクジェットプリントモジュールの開発に使用していると述べています。彼は、コニカミノルタがパナソニックのプリントヘッド事業を引き継いだ後に、パナソニックがすべてのヘッド、すべての顧客の色ごとに波形を調整していたことをコニカミノルタがどのように発見したかを説明しました。「それはもうクレージーですよ!コニカミノルタは、さまざまなアプリケーションで機能する堅牢な波形を生成します。広範囲の流体を扱うことができるため、インテグレーションが容易になります。」
O’Hara says that IIJ has been working with Konica Minolta for around a dozen years, both supplying these printheads to the UK market and using them to develop a range of inkjet print modules. He described how Konica Minolta found after taking over the Panasonic printhead business that Panasonic had been tuning wave forms for every head, for each colour for every customer, adding: ”That’s insanity. Konica Minolta produce robust waveforms that work for a range of applications. Being able to work with a wide range of fluids makes integration easier.”
「ヘッドにはヒーターが内蔵されており、さまざまな粘度に対応できます。」彼は、コニカミノルタが AccurioJet KM1用のゲルUVインクを開発し、これが他の OEM顧客にも利用可能になると指摘しています。「標準のインクシステムよりも複雑なので、もう少しきめ細かいサポートが必要になるでしょう。」
He says: “The heads have built-in heaters and can handle a range of viscosity.” He points out that Konica Minolta developed a gel UV ink for the AccurioJet KM1 and that this will now be available to other OEM customers, noting: “It’s more complex than a standard ink system so there will be a little bit more support.”
O’Haraは、すべてのアプリケーションが高解像度を必要とするわけではないと言って、プリントヘッドにユーザーがどのような機能を求める必要があるのかを問いかけました。彼は付け加えました:「より安いものに対する市場からの要求があります。しかし、このようなものは開発と完成に非常に高価であるため、ノズルあたりのコストに関する一定の疑問が人々を市場から押し出してしまいます。」
O’Hara questioned what sort of features people should look for in a print head, saying that not every application needed high resolution. He added: There’s a demand from the market for cheaper. But this stuff is cripplingly expensive to develop and to make perfect so a constant question of cost per nozzle will squeeze people out of the market.”
彼は、IIJの指針のひとつは、すべてを可能な限りシンプルに保つことであり、次のように付け加えます。「システムが複雑になればなるほど、R&Dコストが高くなり市場投入に時間を要します。そして、システムが複雑になるほど、悪いものを抱え込む可能性が高まります。」このように、IIJはヘッドをまとめ、色間のピニングを避けて非常にコンパクトなプリントモジュールを作成します。
He says that one of the guiding principles at IIJ is to keep everything as simple as possible, adding: “The more complex a system the higher the R&D costs and you will be later to market. And the more complex the system you build the more potential for things to go wrong.” Thus IIJ keep the heads together and avoid pining between colours to create very compact print modules.
その後、O’Haraはコンパクトプリントヘッドを使用することについて良い議論を続け、コニカミノルタヘッドはフットプリントがかなり小さくする傾向があることを指摘しました。これは、より小さなプリントシャトルを実現するため、ワイドフォーマット印刷などのスキャンアプリケーションで重要です。これにより、小さなシャトルを動かしやすくなり、双方向印刷の精度が向上するため、プリンターのコストを削減できます。
O’Hara then went on to make a good argument for using compact printheads, pointing out that the Konica Minolta heads do tend to have a fairly small footprint. This matters in scanning applications, such as wide format printing, because it makes for a smaller print shuttle. This in turn helps to cut the cost of the printer, as its easier to move a smaller shuttle, and it also leads to better bi-directional print accuracy.
また、コンパクトなプリントヘッドを使用すると、ヘッドのノズル列間の距離が短くなり、より小さな回転半径で印刷できるため、平面ではない表面に直接印刷するのに役立ちます。そして、もちろん、プリンター全体が小さければ小さいほど、それを作るのは安くなります。
Using compact printheads also helps with direct to shape printers as it allows for a smaller distance between the rows and therefore the ability to print to smaller radiuses. And, of course, the smaller the overall printer, the cheaper it is to build it.
シングルパスのウェブフィードプリンターでコンパクトヘッドを使用する理由は、色の間でウェブが移動するリスクを減らすためです。当然、印刷ユニットがコンパクトであればあるほど、既存のマシンに簡単に後付けできます。IIJは、コニカミノルタのプリントヘッドを使用して、モノクロユニットよりも大きくない 4色ユニットを含む、非常に効果的な範囲のプリントモジュールを開発しました。O’Haraによると、これは、ヘッドを近づけておくと、アーチのデザインが不要になり、ピニングする必要がなくなり、コストも節約できるためだと言います。
There’s an even more compelling reason for using compact heads on a single pass web-fed printer as it reduces the risk of movement of the web between the colours. Naturally, the more compact the print unit, the easier it is to retrofit it to an existing machine. IIJ has used the Konica Minolta printheads to develop a highly effective range of print modules, including four-colour units that are not much bigger than some monochrome units. O’Hara says this is partly because keeping the heads close together means there’s no need for an arch design, and no pinning between the colours, which also saves on cost.
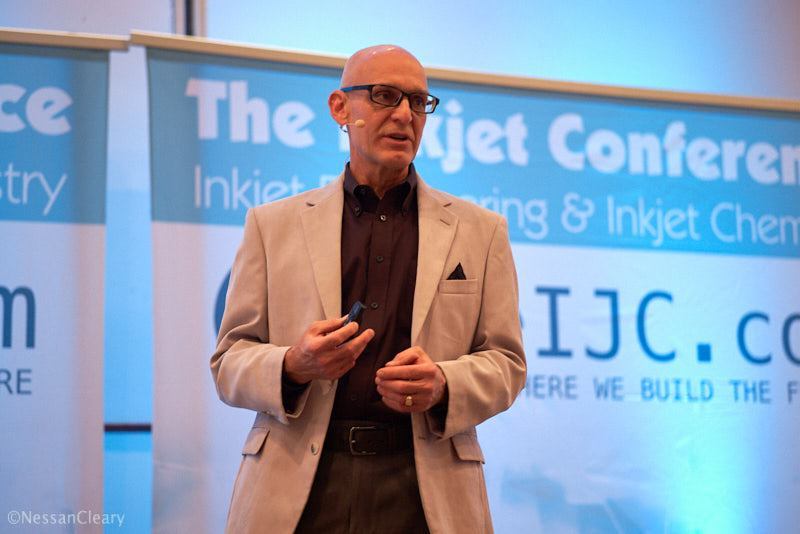
Tom Roetker, vice president of engineering for Memjet
Memjetのエンジニアリング担当副社長 Tom Roetker
Memjetのエンジニアリング担当副社長である Tom Roetker氏は、プリントシステムがどこにフィットされるべきかを考えることの重要性についても語りました。製造工程の中でプリントを行う場所はさまざまな要因によって決まることがありますが、プリントを使用場所に近づける柔軟性を高め、パッケージングに対する工程の後の方でのカスタマイズしたいという需要が高まっています。
Tom Roetker, vice president of engineering for Memjet, also spoke about the importance of thinking about where the print system has to fit into, saying that sometimes various factors dictate where you have to use the printing in the manufacturing chain but that increasingly customers are looking for more flexibility to bring the printing closer to the point of use as well as a growing demand for late stage customisation to packaging.
Memjetは MEMsアプローチを使用しており、近年では、コアテクノロジーに投資して、接着ヒーターや統合温度センサーなどの多くの新機能を追加し、発射チャンバーと流体チャネルの設計を改善しています。ボンディングされたヒーターは液滴サイズを改善し、チャンバーの再充填速度を改善すると、よりまっすぐな液滴噴射が可能になります。
Memjet uses a MEMs approach and in recent years has invested into its core technology to add a number of new features, including a bonded heater and integrated temperature sensors as well as improving the design of the firing chamber and the fluidic channel. The bonded heater has improved the drop size, while improvements to the refill rate for the chambers leads to straighter drop ejection.
これにより、ドロップの着弾精度と各ドロップのボリュームの均一性が改善されました。Memjetは、冗長ノズルの数を大幅に増やすことにも成功しており、これが各プリントヘッドの長寿命化に直接寄与しています。
This has resulted in improvements to the drop placement accuracy and the consistency of the volume of each drop. Memjet has also managed to significantly increase the number of redundant nozzles, which in turn directly contributes to a longer lifespan for each printhead.
Memjetはこのテクノロジーを使用して 2つのプラットフォームを開発しました。Duralinkは、ここで既に説明した高速シングルチャンネルプリントヘッドです。 DuraFlexは私がここで書いた低ボリュームのアプリケーションを対象とした 4色バージョンです。どちらも水性顔料インクを使用し、70,400個のノズルを備え、最大 15.5 KHzの駆動周波数から 2.1plの液滴を吐出します。
Memjet has used this technology to develop two platforms: Duralink, a high speed single channel printhead that I’ve already covered here; and DuraFlex, a four colour version aimed at lower volume applications, which I’ve written about here. They both use an aqueous pigment ink and have 70,400 nozzles, delivering a 2.1pl droplet from a firing frequency of up to 15.5 KHz.
DuraLinkヘッドは、最大 12ヘッドまでずらして 2.5m幅のプリントバーを作成できます。これらのプリントバーは、最大 8色まで使用できるように 8段に積み重ねることができます。Memjetはインクを供給し、既存の CMYKとともにオレンジ、グリーン、バイオレットをリリースし、7色のインクセットを作成しました。DuraLinkヘッドは単色のみを噴射するため、Memjetはノズルの冗長性を劇的に向上させることができました。Memjetは、クローズドループトーン補正も使用します。これにより、印刷画像の問題が自動的に認識され、出力が修正されます。
The DuraLink heads can be staggered, with up to 12 heads to create a 2.5m wide printbar. These printbars can be stacked eight deep to allow for up to eight colours. Memjet supplies the ink, and has just released orange, green and violet, alongside the existing CMYK to create a seven-colour inkset. Since the DuraLink heads only jet a single colour, Memjet has been able to dramatically increase the nozzle redundancy. Memjet also uses a closed loop tone compensation, which automatically recognises problems in printed images and corrects the output.
DuraFlexの設計は、A4および A3 +ワイドヘッドの選択肢を備えたはるかにコンパクトなソリューションを提供し、最大 4つの色をサポートする幅 1.2 mまでの単一の印刷バーを作成するためにずらして配置できます。Roetker氏は、顧客がよりコンパクトな DuraFlexシステムを選択できるようになるということは、「(制約が
あってそこに)行くべき場所ではなく、置きたい場所に置くことができる」ことを意味していると言います。
The DuraFlex design offers a much more compact solution, with a choice of A4 and A3+ wide heads, that can be staggered to create a single print bar up to 1.2m wide that supports up to four colours. Roetker says that giving customers the choice of the more compact DuraFlex system means “they can put it where they want to put it and not where we told them it should go.”
Roetker氏は、MEMs製造プロセスを使用することが印刷品質にとって重要であると述べ、DuraLinkヘッドは 3シグマのドロップ配置で 4ミクロンを噴射できることに留意し、「非常に均一な着弾精度を持っています。」と加えます。
Roetker says that using a MEMs manufacturing process is important to the print quality, noting that the DuraLink heads are capable of jetting 4 micron at 3 sigma drop placement, adding: “We have very consistent drop placement accuracy.”
彼は、Memjetにもある程度のメンテナンスが組み込まれていると言います。「すべてが自動化されているため、印刷の開始時にクリーニングを行うことができます。」これにより、プリントヘッドは交換が必要にも関わらず、依然として寿命を延ばせることを意味します。彼は、プリントヘッドの位置合わせに約 2分しかかからないと説明し、「カメラシステムを介してドライブし、プリントヘッドを 5ミクロンの精度内に調整できる」と説明しています。
He says that Memjet has also built in a certain amount of maintenance, saying: “Everything is automated so we can do a clean at the start of printing.” This has helped to extend the lifespan of the heads though printheads do still have to be changed. He says that it takes about two minutes to align a printhead, explaining: “We drive it through a camera system and can adjust a printhead to within five microns accuracy.”
Roetkerは、Memjetの成功の鍵は、プリントヘッドから製品全体に至るまでシステム全体にアプローチすることだと言います。彼は次のように付け加えます。「インクはエコシステムの一部でもあると考えました。インクとメディアの相互作用があるため、さまざまなメディアに役立つプライマーなどの開発を顧客に支援したいと考えます。」
Roetker says the key to Memjet’s success is to approach the whole system from the printhead all the way through to the whole product. He adds: “We looked at the ink as also being an eco-system component. There is an ink to media interaction so we decided that we also want to help customers develop primers and other things that help with different media.”
これにより、他のベンダーは Memjetソリューションを自社の製品に迅速にインテグレートできるため、コストを削減してより早く市場に参入できます。Memjetは、メンテナンス、インク供給、廃棄物管理、ソフトウェアインターフェイスを備えたプリントヘッドモジュールを提供しますが、OEMはプリンターシャーシ、さらに追加の乾燥とバルクインク供給、およびキャリブレーションと品質管理、RIPとワークフローを組み立てる必要があります。
This allows other vendors to integrate the Memjet solution quickly into their products, so they can get to market faster with reduced costs. Memjet supplies the printhead module complete with maintenance, ink supply, waste management and software interface, while the OEM has to put together the printer chassis, plus any additional drying and a bulk ink supply, along with calibration and quality control, RIP and workflow.
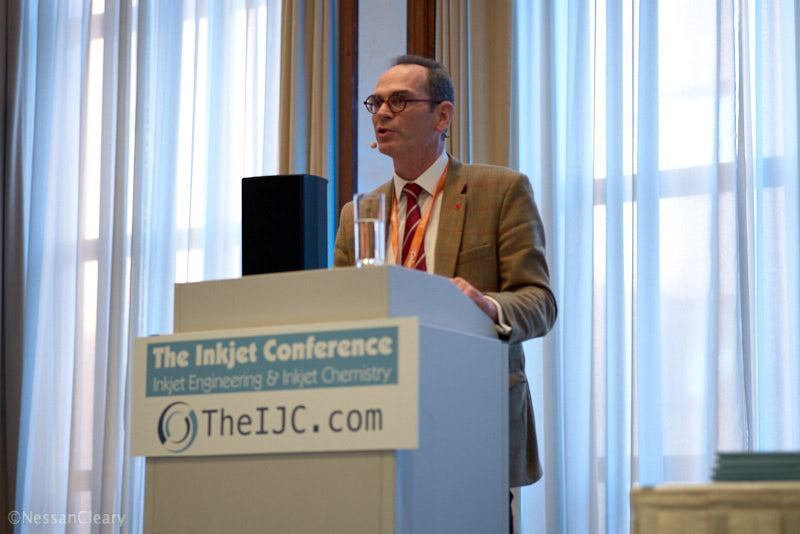
Richard Darling, in charge of strategic business development at Ricoh Europe.
リコー・ヨーロッパの戦略的事業開発を担当するリチャード・ダーリング
Ricoh Europeの戦略的事業開発を担当する Richard Darlingは、NDAについて心配する必要がなく、サプライヤがもっと協力していくべきだという興味深い提案を行いました。これは私が話した一部のベンダーはあまり熱心ではなかった点です。しかし Darlingは、インクジェット技術に莫大な金額が投資されているにもかかわらず、ほとんどの産業市場にほとんど浸透していないという重大な指摘をしました。彼は次のように述べています。「人々はドロップサイズに興味はありませんが、お金を稼ぐ方法に興味があります。我々がなんらかのリターンを提供しない限り、このテクノロジーへの投資は枯渇してしまうでしょう。」彼は、「何か見返りを提供することなく、10のパフォーマンス向上に、に予算の 90%を費やし続けるとしたら、それは重大な間違いです」と付け加えました。
Taking a different tack, Richard Darling, in charge of strategic business development at Ricoh Europe, made an interesting pitch that suppliers should work together more and worry less about NDAs, which some of the vendors I spoke with were less keen on. But Darling did make a serious point that inkjet technology is still only barely penetrating most industrial markets despite the huge sums of money that have been invested in it. He said: “People aren’t interested in drop size but in how they make money. Unless we deliver a return the investment in this technology will dry up.” He added: “If we continuously want to work on the extra 10 percent of performance that costs 90 percent of the budget without delivering something then we are missing a trick.”
彼は、単に従来のシステムを置き換えようとするのではなく、既存の技術を利用し、インクジェット生産の固有の利点を理解するように顧客を教育する方が良いと提案しました。また、インクジェットを使用することで在庫管理が改善され、従来の生産速度に合わせる必要が少なくなる例を共有しました。
He suggested that it would be better to educate customers to make use of the existing technology and to understand the inherent advantages of inkjet production, rather than simply seeking to replace conventional systems. And he shared examples where the use of inkjet allowed better inventory management so that there was less need to match conventional production speed.
これまでのところ、私は毎日の始めから全体会議のプレゼンテーションのいくつかだけを描いてきました。しかし、インクジェットプリントシステムで共に機能する、プリントヘッドの設計、インクの化学的性質、ソフトウェアなどのさまざまな側面をカバーする非常に多くのプレゼンテーションがありました。これらのプレゼンテーションのいくつかについては、今後数か月にわたって、波形設計、ノズルを通過するインクの再循環、MEMアーキテクチャの使用、高粘度流体を扱う Xaarの取り組み、富士フイルムの Sambaなどに関する更なるストーリーを取り上げます。これらの物語に興味のある方は来年の IJCへの参加を検討することをお勧めします。詳細については theijc.comをご覧ください。
So far I’ve only drawn on some of the plenary presentations from the start of each day. But there were a great many more presentations covering the different aspects of printhead design, ink chemistry, software and so on that together play a part in an inkjet printing system. I’ll come back to some of these presentations in further stories over the next couple of months dealing with issues such as waveform design, recirculating ink past the nozzles and the use of MEMs architecture as well as Xaar’s work in jetting high viscosity fluids and Fujifilm’s Samba Printheads. In the meantime, I’d suggest that anyone interested in these stories might want to consider attending next year’s IJC – you can find details at theijc.com.