- 2024-2-26
- Nessan Cleary 記事紹介
2024年2月23日
ここ数年、富士フイルムはカリフォルニア州サンタクララにあるディマティックスの製造工場を静かにアップグレードしてきた。そこで私は、MEMs製造工程がどのように機能しているのか、そしてそれがプリントヘッドにとってどのような意味を持つのかをよりよく理解するために、工場を見に行った。
Dimatixには 2つの製造施設があり、どちらもアメリカにある。同社の主要拠点はニューハンプシャー州にあり、StarFireシリーズや Saphireシリーズなど、富士フイルムのプリントヘッド・ポートフォリオのほとんどを製造している。アメリカのシリコンバレーの中心にあるサンタクララ工場は、それとはまったく異なる提案をしている。この工場は、MEMs(MicroElectrical Mechanical Systems)アプローチを採用するために設立された。基本的にこれは、アクチュエーターを構築するために半導体技術を使用することを意味し、より複雑で高精度を可能にする。
事業開発担当 EVPのベイリー・スミスが指摘するように、これはシリコンバレーに拠点を構えることを意味する: 「MEMをやろうと思えば、できる場所は2、3しかありません。シリコン MEM施設は、こことシリコンバレーに山ほどあります。窒素ガスや化学貯蔵の専門知識が必要です。ニューハンプシャーでそのような人材を確保しようとするのは不可能だったでしょう」。(この工場では、電子回路の銅が酸化するのを防ぐため、製造装置内に無酸素雰囲気を作り出す液体窒素を大量に消費している)。
1984年に設立されたディマティックスは、まだマーケム・コーポレーションの傘下にあったころ、MEMへの投資を決断した。MEMへの投資を開始するため、同社は当時すでに 10年前のシリコン製造装置を手に入れた。
同時に富士フイルムは、デジタルがいずれオフセット印刷に取って代わることを認識し、CTP事業に代わる方法としてインクジェットに注目していた。そのため、富士フイルムはすでにインクジェット印刷機 JetPressの開発作業を開始していた。その結果、同社は 2005年に UVインクを開発する Sericol社を、2006年には水性インクを専門とする Avecia社を、そして同じく 2006年には Dimatix社を買収するに至った。スミスは言う: 「富士フイルムの核心はテクノロジー企業です。彼らは生産している製品の技術を所有したいのです」。
彼は続ける: 「彼らは JetPressに高い印刷品質が必要であることを知っていましたし、すでに日本で MEMに取り組み始めていました。しかし、私たちがやってきたことを見て、彼らは興味を持ったのです」。
ディマティクスの MEMへの最初の取り組みは、バルクピエゾが中心だった。しかし、富士フイルムはすでに別のアプローチ、スパッタリング PZTを開発していた。スミスはこう説明する: 「日本の富士フイルムが核となる特許を持っており、その技術をライセンス供与してもらいました。また、ツールのカスタマイズも行いました」。
スパッタリング PZTは、プリントヘッドの MEMs製造に使用できるいくつかの方法のひとつであることを指摘しておく。他のプリントヘッド・メーカーが採用しているソルゲルなどの方法とはまったく異なる。スミス氏は、スパッタリング PZTはより堅牢で、工業生産に適したヘッドにつながると言うが、もちろん他のメーカーも自社のヘッドについて同じことを言うだろう!
今日のピエゾ式ドロップオンデマンド・プリントヘッドのほとんどは、通常 PZTと呼ばれるチタン酸ジルコン酸鉛を使用している。PZTは、電荷を加えると形状が変化する、非常に効率的な圧電特性を持つからだ。ピエゾ式プリントヘッドは、この形状変化を利用してインクをインク室からノズルへと押し出す。
富士フイルムのアプローチは、RFマグネトロンスパッタリングの一種を使用してシリコン基板上に薄い PZTフィルム層を形成することで、従来の PZTフィルムよりも約 70%高いピエゾ電気係数 d31=-250pm/Vを実現している。これは、約 13%という高レベルの Nbドーパントを使用したことと、PZTの歪み方を制御するために不可欠な結晶の並び方を非常に正確に制御したことによるところが大きい。
スミスは、ソルゲルを含む他の技術に対するこのアプローチの大きな利点は、PZTのポーリングにあると言う。私たちが開発したスパッタリング・プロセスはユニークです。バルクのピエゾでは、塊を入れて結晶を形成し、それを非常に高い温度でポーリングして整列させなければなりませんが、これは非常に難しいことです。私たちの PZTを蒸着させると、すでにアライメントされているので、高温処理は必要ありません。
彼は続ける: 「ある波長からどれだけ偏向させることができるかが、我々の尺度のひとつです。また、温度をかけすぎると極性を失うこともあります。私たちは最高のPZTを持っていると感じています。
彼はこう付け加えた: 「スパッタリング PZTを使ったMEMの他の潜在的な応用について研究開発する少人数のグループがあり、この種の仕事では世界的に有名です。ニューハンプシャーで製造される製品の開発の一部をここで行っています。エンジニアリングと開発だけで、生産はしていません。超音波の分野や医療機器も手掛けていますが、主要な分野ではありません」。
より大きなウェハー
マイクロ・エレクトロ・メカニカル・システムは、エレクトロニクスと可動部品を組み合わせたもので、非常に小さなスペースで複雑な設計を実行することができる。このようなシステムを構築するための材料の選択肢は限られており、耐用年数が長く、電子機能を組み込むのが容易なシリコンが圧倒的に一般的である。その結果、Si-MEMは半導体デバイスの製造と同様のプロセスで製造することができる。そのため、PZT薄膜付きシリコンのような材料は、一度に 1層ずつ堆積させることができ、フォトリソグラフィーを使ってこれらの層内にパターンを作り、電子回路や流体管理のためのチャネルを作ることができる。
プロセスはフォトリソグラフィーから始まる。スミスはこう説明する: 「半導体のプロセスです。半導体のプロセスです。ですから、複数の層を経てプロセスを構築していきます。20層ほどのレイヤーがあり、各機能はこれらのさまざまなレイヤーで追加されます。各フィーチャーを 1つずつ追加していきます。そして、それを積み重ね、メタライゼーション(金属化)を行います」。これらの機能には、再循環のための流体管理用の別レイヤーも含まれる。
この作業は、オランダから供給された ASMLステッパーで行われる。スミスは言う: 「ASMLは、台湾の TSMCに次いで世界最先端です。
このフォトツールは、レイヤーの両面にパターンがあるため、表面のフィーチャーと裏面のフィーチャーを合わせなければならないからです。そのため、特殊な処理が必要になります。ウェーハの底面を傷つけることになるので、ウェーハの両面を保護する必要があるのですが、ASMLのステッパーは非常に信頼性が高いのです」。
富士フイルムディマティクスの MEMs研究開発担当副社長、ダレン・イマイ氏はこう指摘する: 「これらは非常に繊細な構造で、約 400ミクロンから 650ミクロン、時には 10ミクロンに及ぶこともあります」。
ここ数年、富士フイルムは、6インチから 8インチまで、より大きなウェハーを製造するために、いくつかの製造ツールを適応させてきた。Sambaプリントヘッドの基礎となるダイは、これらのウェハーから直接切り出される。つまり、ウェーハサイズが大きくなることの直接的な利点は、製造能力の向上である。6インチウェーハでは 10個のダイを得ることができるが、8インチウェーハでは 21個になる。
この生産能力増強に加えて、装置のアップグレードはより良い結果をもたらしたと今井は説明する: 「8インチウェーハでは、6インチウェーハよりもはるかに効果的にPZTの均一性を得ることができました。より大きなウェハーへの変更には、かなりの資本と多大な努力が必要だったと今井氏は言う: 「プラットフォーム全体の均一性が向上しました。多くの装置をアップグレードし、中には30年前のものもありました。私たちは、より多くのプロセス上の利点をもたらす、より最新鋭の設備を導入しました」。
より大きなウェーハサイズに移行する際の課題の 1つは、装置をアップグレードする一方で工場での製造を継続する必要があったことであり、そのためサイズも 8インチに制限されていた。富士フイルムは、8インチウェーハに対応するために既存の装置をアップグレードすることができたが、それ以上のサイズではゼロから始めなければならなかった。
ダイはサンバプリントヘッドの基礎となるもので、エレクトロニクスと流体チャンネルを含んでいる。しかし、他の部品も追加しなければならないため、これがすべてではない。ダイの前面にはノズルプレートがある。背面にはインク流路と電子接続部がある。
もう一つの重要な部品は、ヘッドを最小限の手間で正しく取り付け、アライメントできるようにする取り付けブラケットである。また、EPROMモジュールもあり、電圧係数やテスト、ヘッドグレードなどのパラメーターが含まれている。サンバのプリントヘッドを 1つ作るのに約 3ヶ月かかる。
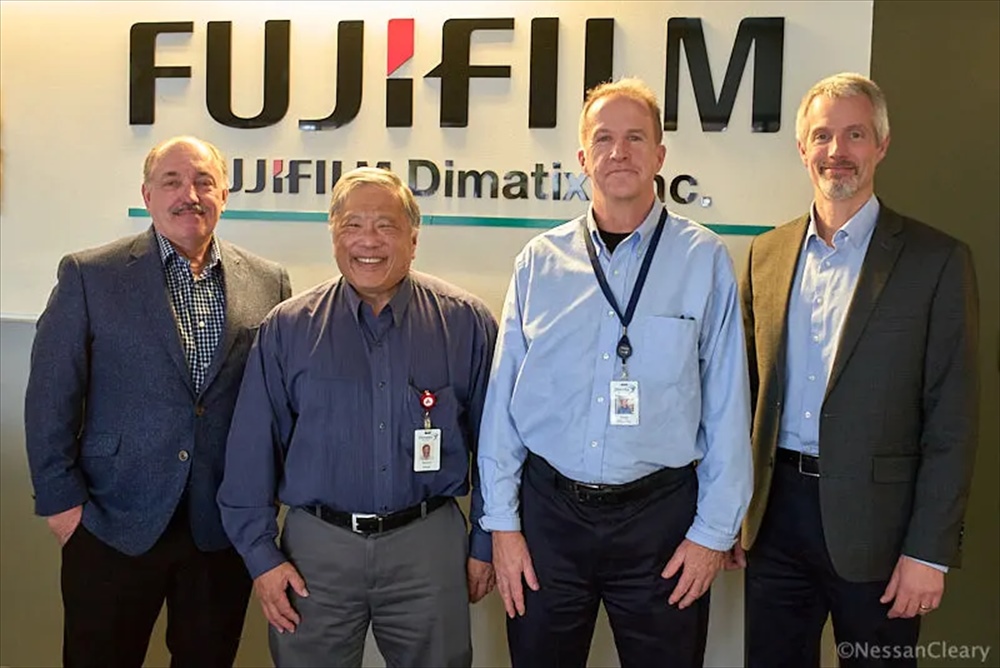
左から オペレーション担当副社長 Dave Pulizzi氏、MEMs研究開発担当副社長 Darren Imai氏、シニア・プロダクト・マネージャー Terry O’Keefe氏、EVPビジネス開発担当 Bailey Smith氏
Sambaプリントヘッドのシニア・プロダクト・マネージャーである Terry O’Keefe氏は、MEMs製造は Sambaの機能セットの本質的な部分であると語る: 「液滴がますます小さくなり、乱流によるあらゆる問題が発生するため、ノズルをできる限り近づけたいと考えています。そして、高速で運転すればするほど、すべてのことが重要になってくる。そして、これらの機能をすべて小さなスペースに配置できることが、MEMの特徴のひとつなのです」。
オキーフは、材料セットは顧客が使用する多くの流体と化学的に互換性がなければならないと言う: 「私たちはすべてを自社で行っています。設計からテストまですべて自社で行っています。当社にはジェット設計の専門家がいます。プロセスを通してテストし、情報を得ることができます」。
スミスは詳しく語る: 「私たちは材料試験に力を入れています。出射の性能を予測できるようになりたいのです。液滴の生成には多くのエネルギーが必要ですが、それによってノズル間のフィードバックやクロストークが発生します。私たちは、市場のどの製品よりも優れた多くの製造ツールを開発しました」。
結論として、サンタクララにあるディマティックスの工場は非常に印象的である。この工場は、ほぼ完全に Sambaプリントヘッドの製造に専念している。施設全体は 24時間 365日稼働しており、約 300人が働いている。天井にはパイプとケーブルが張り巡らされ、専用のクリーンエリアを含む各工程専用の部屋がある。最近の更新により、ディマティックスは 2027年までのニーズに対応できる十分な能力を確保した。サンタクララ工場の運営担当副社長であるデイブ・プリッツィ氏は、「必要な場合には、それを超える計画も立てています」と語る。
この記事にはまだ続きがあり、Sambaヘッドと、MEMsアプローチを追求するという富士フイルムの決定からどのような恩恵を受けているのか、そしてそれが現在のシングルパスインクジェット印刷機にどのように反映されているのかについて、さらに詳しく見ていく予定である。詳細は fujifilm.comをご覧いただきたい。